The end of the brick age? Making the energy transition in brick manufacturing
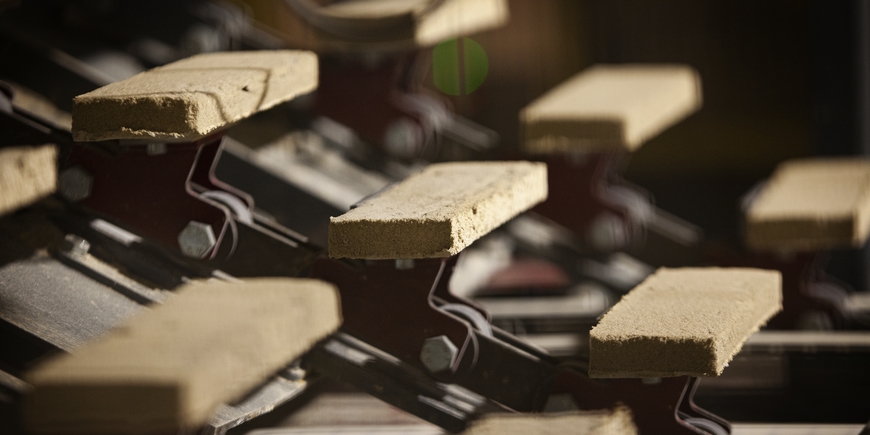
Does the brick still have a future now that Europe has drawn the map of a CO2-neutral economy by 2050? It’s a valid question. After all, everyone knows that bricks are baked in an oven and needs energy. So, will brick manufacturing continue?
The brick of the future
The answer is a resounding yes. Brick is alive and kicking as a building material. Even in these strange times, we keep looking ahead, working on our distant and not-so-distant plans for the future. At Vandersanden, we are especially proud that we don't think in years, but in generations, and I am very confident that the next generation will also be producing bricks.
The facade brick, and our industry, will change profoundly in the years ahead. Energy efficiency is an important driver for buyers, project developers and suppliers. We are already planning and implementing this transformation because it is our ambition to be at the forefront of sustainability.
We see the transition taking place in two steps. In the first phase - by 2030 - we want to drastically reduce the energy emissions of our facade and paving brick production.
Then we set the horizon for 2050. By then, we will have achieved a 100% green, energy-neutral baking process.
2030: a slimming cure for the facing brick
Brick is a very durable building material. It is made from natural, often recyclable, raw materials, such as, clay and sand. During the production of bricks, we create almost zero waste. In this production process, we do emit CO2: during firing, but even more so in drying. In figures: Vandersanden emits around 60,000 tons of CO2 annually from its Belgian facing brickworks (Bilzen and Lanklaar) and around 25,000 tons from its Dutch facing brickworks in Beek and Hedikhuizen.
This is only a very small percentage of the industry's total annual CO2 emissions (18 million tonnes per year in Belgium) and that's why we are not obliged to minimise it. However, when it comes to sustainability, we believe that we all have a figurative contribution to make. How do we do that? The most important evolution today is that the facing brick goes on a diet, this is called 'dematerialisation' (narrower facing bricks). In its most extreme form this means you go from facing bricks to brick strips.
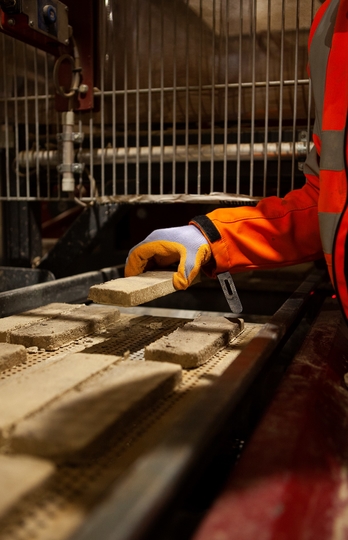
Energy saving and sustainability
A standard facing brick measures 10cm today. The time when our facades were covered with a layer of 10cm stone is behind us. Today, we are evolving towards bricks of 6.5 to 8cm deep. You save on materials, but you also need significantly less energy in the production process. Some variants are not so much thinner but have less material due to recesses in the stone. However, you always come up against the limit of 30% savings.
The slimming process does not stop there. Vandersanden has already used the movement to make 1.8cm brick strips. You can obtain those strips by sawing full bricks into strips, but Vandersanden was the first brick manufacturer to switch to the production of ECO brick strips, which are currently formed in 1.8cm moulds.
With the current 1.8cm stone strips that are formed in the mould, the use of raw materials decreases by more than 70% compared to traditional facing bricks. Energy consumption is currently reduced by 50% as the strips are laid in cassettes for firing in a tunnel kiln. Vandersanden wants to bake these strips in a 'roller oven' in the near future so that energy consumption will also be reduced by 70%.
By using less material, we not only save energy and raw materials, but also drastically reduce the emissions from transport. And, by using thinner bricks and/or brick strips, you have more space for insulation in your walls.
Low-CO2 facing bricks are actually within reach thanks to the evolution towards ECO brick strips that are baked in a roller oven. As a result, it is no longer so difficult to take the next step to achieve a CO2-neutral or even zero-emission brick. Given the CO2-intensive production of bricks based on fossil fuels, this is still future music today.
By 2050, however, we want to have solved this challenge, although we still have a number of licensing hurdles to overcome, such as, the possibility of producing green electricity via wind turbines.

By using less material, we not only save energy and raw materials, but also drastically reduce the emissions from transport.
2050: CO2-neutral, by greening the production process
Based on the new standard of dematerialised stone, we know that we will need less energy in our process in the future. Then, it will be easier to completely replace it with renewable energy.
We are already making maximum use of existing technology. We have installed solar panels on all factory roofs. We are also planning a first wind turbine at our Lanklaar site. But, obtaining permits for wind turbines is proving to be a very challenging process today. And, in our paving brick factory in Tolkamer, we recently have a new extremely economical oven, which replaces three older baking ovens and reduces energy consumption by approximately 30%.
We are also investing in new technological breakthroughs. Hydrogen could be very interesting if we can extract it from wind or solar energy. We are not waiting for that to happen, but we are sponsoring an innovative study project at KU Leuven to produce hydrogen gas with high efficiency by means of solar panels.
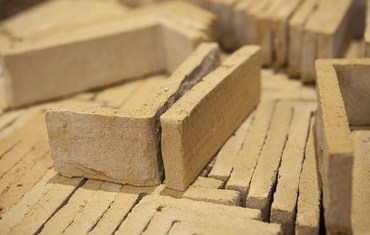
On our way to producing CO2-negative bricks
CO2-neutral is the clear way to go for the coming years. Thanks to brick strips and the greening of our production process, we at Vandersanden are well on the way to producing at least CO2-neutral by 2050 at the latest. We even hope to meet the zero-emission standard.
But, here too, we do not stop at our production process. We also include the product itself in our path to climate neutrality.
After all, we are currently well on our way to producing CO2-negative bricks. These are bricks that do not emit CO2 during the production process, but - on the contrary - absorb CO2. Since a large part of the basic raw material comes from recycling, we are also taking a first step towards a "circular" economy. This CO²-negative stone becomes completely circular if we succeed in processing it "dry-stacked" (instead of gluing or masonry) in such a way that the wall can be dismantled and the bricks reused when demolished. The first product developments of this "disruptive facing brick" are promising.
In any case, let it be clear that Vandersanden does not stand still when it comes to sustainability. For us, the decorative facing brick must keep up with the times. Thinner and, therefore, low-CO2 or eco-friendly facing bricks are the first part of the puzzle.
You can count on us to give the construction sector the necessary push to contribute to the energy transition in the brick industry.